5 basic questions for a smarter purchase
Okay, you’ve done the hard part. You’ve created a great product with overwhelming customer appeal.
Maybe it is a bakery snack, maybe a unique hardware item, maybe it’s a medical device – it could be almost
anything. But, if you are like most product developers, you face a common challenge that is sometimes left unresolved until the end of the development cycle. You need to package your product. The importance of an excellent package cannot be overstated, and great products deserve great packaging. And, the extra effort spent in planning your packaging system purchase will pay ten fold if done properly.
Address the following five basic questions and you will be well along the path to a smart purchase decision that will pay dividends for years to come.
- What’s in the bag?
Though it may seem obvious, the first question is this: what are you planning to package? Cookies, for example, will require a different set of criteria (bag material, machine type, packaging process, etc.) than a medical device, a piece of cheese, a hardware item or a silicon wafer. How long will the product remain in the package? Is microbial contamination an issue? Is the product susceptible to damage from static discharge? Will the contents need vacuum packaging? Will the product require modified atmosphere packaging (MAP)? Understanding how the contents of the bag can and will affect the packaging can go a long way in determining the packaging process required, the bag style, bag material needed and the most appropriate choice in packaging equipment.2. Which bag?
Choosing the correct bag type and bag material is the logical next step. Standard bag materials generally include low and high-density polyethylene, DuPontTM Tyvek®, polyester, polypropylene, poly nylon, plus various combinations of foil or paper laminated to plastic. Bag styles include bags on a roll, pouches, stand up pouches, wicketed bags, pillow, bags that are fabricated from rolls of sheet film (on a flow wrapper machine), and others – with new bag and pouch designs appearing with increasing frequency.Let’s start with a common application: dry brownie, or cookie mix. If your application falls under this general
category your main concern should be keeping the ingredients fresh and free of microbial contamination. Many modern packaging professionals are turning to stand up pouches for this type of dry ingredients, as these bags are resistant to puncture, oxygen, moisture, and UV light, which all contribute to the degradation of dry baking products. These thick, sturdy bags feature multiple layers of barrier film that have been laminated together. The benefit here is that your food remains fresh and safe for an extended period of time, consumers enjoy the convenience of a reclosable “stand-up” pouch, and retail shelf appeal is improved. When the customer consumes the product, the results are better, higher levels of customer satisfaction are achieved, and your product is on its way to establishing improved brand loyalty. Packaging can be accomplished through the use of semi-automatic band or impulse sealers, or automatically using a horizontal or vertical form-fill-seal machine.Medical device, personal-care and cosmetic packaging face a very different set of criteria. Packaging engineers in these markets work in a fast-moving environment as new regulatory guidelines are established and advancements are made continually in the field of packaging styles and materials. For many medical applications, peelable Tyvek sterilization pouches are the bag of choice. Tyvek sterilization pouches are often constructed from either 1073B Tyvek or 1059B Tyvek. A polyester/polyethylene laminate may also be used as part of the construction. For some applications, breathable sterilization bags are the best choice. This type of pouch is available in a variety of sizes with films made of linear low-density polyethylene or poly/nylon/poly film for enhanced strength and clarity.
Ready-to-eat bakery items, candy bars and snack foods require an entirely different packaging process and bag material. These products are easily packaged using continuous roll film material (often polypropylene, polyester or foil laminates) on a purpose-built conveyorized machine. The bag material is automatically formed into shape, the product is inserted and the package is sealed on three sides and trimmed. The variety of bag, bag size and material combinations is nearly as numerous as the types of products to be packaged.
Performing the essential due diligence when it comes to choosing the best bag style and material for your specific application will save headaches, eliminate process and manufacturing difficulties, deliver better end-user results and save money.
3. Which packaging process?
The process required for packaging your specific product is an important consideration. Packaging a small, metal or plastic product will require a distinctly different process than a cosmetic product or a perishable food. In the instance of the metal or plastic product, you may choose from something as simple as an automatic bagger that uses pre-opened bags on a roll. The bag advances to the feed position where it is opened with a short burst of air, the operator drops in the product and the machine then heat seals and trims the bag. Simple and efficient. Packaging perishable foods require something entirely different.Everyone knows that packaged food does not stay fresh forever, and a number of factors contribute to food spoilage. Oxygen in the air is a common cause of decay. Fats and oils in food can come in contact with oxygen over a prolonged period of time causing the food to become rancid. One of the main causes of food spoilage is the growth of bacteria, yeasts and molds that are present all around. These microbes can feed and grow on the food product, causing it to degrade. The appearance of food can also change over time when exposed to light and air. There are a number of ways to slow spoilage and to keep food attractive and edible for as long as possible. One of the best ways to mitigate spoilage is the use of Modified Atmosphere Packaging (MAP). MAP packaging replaces the air contained in the package with a mixture of natural gases in carefully controlled proportions that can significantly slow down the process of decay. These gases inhibit oxidation and the growth of harmful microbes. The type and proportion of gas used in the packaging is largely dictated by the type of food in the package and the sort of decay or change that the food undergoes. To package a product in a modified atmosphere requires a nozzle-type vacuum sealer or a vacuum chamber that removes the air from the bag and replaces it with a carefully defined recipe of gases, then seals the bag so only the modified atmosphere gas surrounds the product.
4. How rapidly do you plan to package?
The intended speed of your packaging operation has great bearing on which packaging system you invest in. Today, highly automated packaging systems are readily available. These costly machines can operate at incredible speeds, and they are a marvel to watch in use. But not everybody needs this high level of manufacturing capacity. In fact, many packaging systems are neither used every single day nor at maximum capacity – so choosing a machine that closely matches your operational production levels is an important consideration. For example, band sealers suited for medical device applications are available to fill the gap between labor-intensive manual methods and the very expensive, automated, form-fill-seal processing used in a high speed, high volume packaging operation.5. How do you choose the right equipment supplier?
Packaging equipment suppliers abound – but choosing the right supplier for your specific requirement can get tricky. Reputation is a standard rule-of-thumb, but there are other important questions to ask and answer before you commit to a supplier and a system. Has the supplier been in the business for a long time? Does the supplier have a large installed base? Are current customers happy with their equipment? Does the manufacturer specialize in the process you require? Are replacement parts widely available? Is support staff qualified and available to help when needed? Can the supplier work with you on a customized solution or configure a system to meet your unique requirements?Answering all these questions entitles a packaging equipment manufacturer to make the first cut. But, the selection process is not over by any means. How does the manufacturer compare on price and features? It is important to note that a manufacturer’s sell price is not always a reliable metric for choosing a system. A system with a small price can easily turn into a big (and costly) headache.
More important than the purchase price is the total cost of ownership (TCO). TCO is a financial estimate that is intended to help buyers and owners determine the direct and indirect costs of owning and using a particular product or system. For manufacturers, TCO goes well beyond the initial cost of the product. TCO includes a variety of additional “cost-of-doing-business” items, including: energy consumption, repair and maintenance, customer support in a common language, operator training, and other variables, which may include tax credits, and product delivery speed. All of these factors must be considered before the supplier is chosen.
Making an intelligent packaging system purchase is integral to a more successful and profitable business.
Great bagging, packaging, and bag sealing systems can remain in service for many years and require only routine maintenance. Get good answers to these 5 key questions before you make your purchase and you will be ahead of the curve when it comes to making the right choice.
Excellent packaging is achieved by satisfying just a few important requirements: choosing the right bag and bagging material, using the appropriate process, selecting the proper machine to do the job, and choosing the right equipment and material supplier.
Baggers
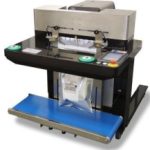
Sealers
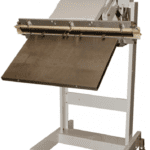