Packaging Story
A compact automatic bagger that unlocks a vast global opportunity.
A compact automatic bagger that unlocks a vast global opportunity.
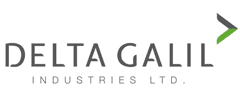
Headquartered midway between Tel Aviv and Haifa on Israel’s picturesque Mediterranean coastal plain, Delta Galil has established itself as a manufacturing leader in the global fashion industry. Designers and retailers worldwide rely on Delta Galil’s industry know-how and manufacturing expertise to help them introduce new trends in their growing markets. By manufacturing a wide range of made-to-order products, from intimates, and activewear to kid’s wear, the company has contributed to the success of some of the world’s most influential retailers, including Nike, Victoria’s Secret, and Calvin Klein, to name but a few. With many global licensing agreements, Delta Galil products are offered under leading brand names like CK Kids, Columbia, Wilson, Maidenform, Tommy Hilfiger, and several others.
Like most apparel manufacturers, Delta Galil’s Southern California distribution operation pays special attention to its product packaging procedures. Precious margin is consumed very quickly if packaging efficiencies are not carefully maintained. Labor costs can be high, and this is where packaging automation can prove significantly beneficial. At the California distribution center (where labor costs are relatively high), apparel was packaged in an inefficient yet remarkably common manner. Single items were placed in a flat poly bag, opened, filled, sealed, and then labeled. The entire 4-step procedure was done by hand. Even with agile, experienced packaging personnel, the process was slow and exceedingly inefficient. As the direct to consumer business at Delta Galil grew, the hand packaging line required more staff to keep up. It was becoming an expensive bottleneck that was starting to eat into already tight margins. Hand packaging had become unsustainable, and it was time to search for a solution.
The search was on to support steady growth, the packaging experts at Delta Galil decided to take a fresh look at their packaging practices, and the obvious first step
was to attend the leading professional packaging exposition in the Western United States: WestPack in Anaheim, CA. WestPack exhibitors included more than 1,500 leading suppliers of advanced packaging equipment, materials, containers, automation technologies, and other supply chain solutions. The expo brings together suppliers of the latest packaging solutions for global companies, start-ups, and everything in between. Attendees included corporate, general, plant, and project managers; engineers; production supervisors; those involved in operations and quality control; purchasers; package designers, brand managers, and marketers
from what seems like every industry. Here, the Delta Galil delegation lead by a distributor, learned a bit about PAC Machinery and several other packaging equipment manufacturers. After a comprehensive survey of the expo, there was a machine at the PAC booth that caught their collective eyes: the Rollbag™ R785 automatic Bagger.
Material benefits
Greg Berguig, VP of Sales and Marketing at PAC joined the conversation and offered up more when it came to benefits. He mentioned that PAC also manufactured a new bag material. Berguig suggested pairing its versatile Rollbag R785 Automatic Bagger and their new Rollbag Recylene™ brand mailer bag material which features 50%+ recycled content. This new material compound is designed for order fulfillment bags; it is exceedingly strong yet uses thinner gauge material. This unique machine/material combination is an environmentally-friendly, sustainable approach to e-commerce fulfillment.
After careful consideration, Delta Galil decided to purchase two Rollbag R785
Automatic Baggers. The machines were built and delivered to the Southern California facility on time as promised. The machines were up and running quickly, and they significantly reduced the labor demand for hand packaging apparel – as promised. As anticipated, the implementation of the two automatic baggers virtually eliminated the hand packaging bottleneck.
How do you measure success?
The successful implementation is summed up in a simple statement from Delta
Galil’s Jeff Lewis: “Our machines are running great. We had our CEO here last week and he approved purchasing the two additional new machines. What are the lead times for the new machines and bags?
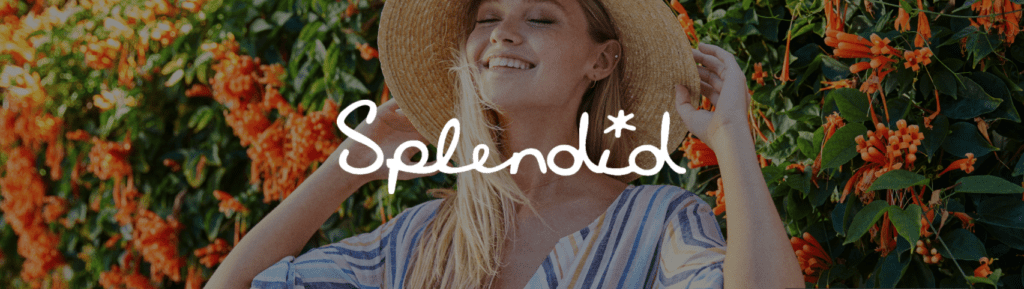
“Until now, e-commerce fulfillment packaging operations lacked a bag material that utilized a high percentage of recycled material in its formulation. Conventional poly bags typically contain a small percentage of recycled content (often derived from the waste material in their own manufacturing process); this content is usually in the single digits. Conventional material thickness is around 3-mil, depending on the manufacturer”, reports Greg Berguig. “Our new Recylene material uses a special blend of consumer and industrial recycled material that exceeds 50% of the total bag material content. We believe the use of our newest bag material, which is thinner (by >30%), and stronger, is a winning combination for Delta Galil. I believe it will appeal to their environmentally-conscious customers.”
Greg Berguig, VP Sales, PAC Machinery Tweet
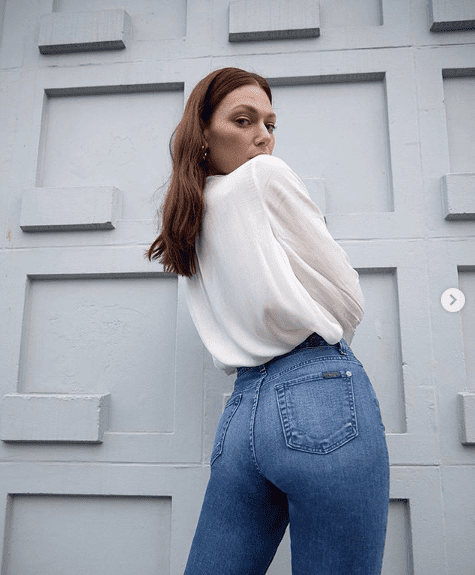