Packaging Story
Large-scale packaging integration serving small-scale humans
Large-scale packaging integration serving small-scale humans
The Phillips-Medisize automation strategy needed to encompass injection molding, assembly, product packaging, bar and lot code printing, insertion into a shipper carton and delivery to a case former.
Hudson, WI-based Phillips-Medisize is a global leader in the design and manufacture of advanced molding and assembly systems; the company has become a leading force in the medical device, drug delivery, and primary pharmaceutical packaging markets. While many of their solutions represent the cutting edge of med device manufacturing technology, some are manufacturing improvements that are applied to decades-old products. Case in point: the ubiquitous baby pacifier. Phillips-Medisize wanted to develop an end-to-end automation system for the production of baby pacifiers – and the automation strategy needed to encompass injection molding, assembly, product packaging, bar and lot code printing, insertion into a shipper carton and delivery to a case former. It was an ambitious project with lots of moving parts, but accomplishing the feat could result in significant labor savings.
A Regional Sales Manager for PAC Machinery, was invited to submit his ideas for a key part of the solution. His part of the puzzle was conveying the molded products into the bagger, sealing the pacifiers in a colorful retail bag, printing bar code information on the bag header, gathering the pacifiers into lots of 250 products, filling cartons and conveying the filled boxes to the case former. The goal was bagging 25 pacifiers per minute. PAC had an idea: “I envisioned a system whereby the pacifiers came off the molding equipment directly into a bowl feeder, which deposited the product into one of our Rollbag R1275 automatic baggers. There they would be sealed, have the barcode applied, fill the carton to the correct quantity and move the box to the case former. The rest of the automation was a job for someone else”.
As the solution unfolded, there were challenges. The soft nipple of the pacifier had a tendency to hang up on the bowl feeder, impeding the flow of product to the automatic bagger. With a few adjustments, the vibratory feeder was configured to orient the pacifiers properly without any binding. The next challenge was an interesting one. “We engineered a special 10’ indexing conveyor to move three boxes at a time from the case former to the auto bagger. But as the pacifiers fell from the bagger to the box below, we ran into a predictable problem: the pyramid effect – with the peak of the products extending above the top of the box,” explained PAC’s product manager. The solution was easy to envision but a bit harder to design. The PAC Machinery engineers worked with Phillips-Medisize engineers to integrate a shaker device into the conveyor that gently shook the box causing the 250, bagged pacifiers to settle nicely beneath the box top. The conveyor would next index the carton, move it to the next position at the carton sealer, and signal the bagger that it was ready for the next cycle. Problems solved.
Phillips-Medisize partners with its customers to provide design and development services, which accelerate speed to market by virtue of advanced automated assembly and quality control technologies. The result is reduced manufacturing cost and improved quality. PAC Machinery proved once again that packaging integration experience & ingenuity could save the day with big solutions that serve the smallest among us.
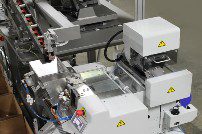
"I envisioned a system whereby the pacifiers came off the molding equipment directly into a bowl feeder, which deposited the product into one of our Clamco."
A PAC Regional Sales Manager Tweet
For more info about the Rollbag R1275 Automatic Bagger, Click here: